
You could call this project a spoon, but I consider it a spatula. It has no bowl, requires no concave blade (like a hook knife), and can be carved completely with a drawknife and very little skill. How’s that for a fun project? I gave a demo on this process some time back at the woodwork shop and I promised to write about it. The promise was almost broken, but since I have not received any complaints, I guess it is ok that this post took a few months.

I’ll just jump right in. The process is best started with firewood of some type. Fruit woods work great, but lots of other woods work, too. Stay away from oak or other “ring porous” hardwoods because the pores can harbor bacteria. Anyway, split that chunk of firewood by any means available to you. Here I am using a wedge, maul, and hardware store handsaw.

Keep working the wood into smaller pieces. Wood likes to split in half. As the pieces get thinner a froe can be very helpful, but not necessary in pieces this short.
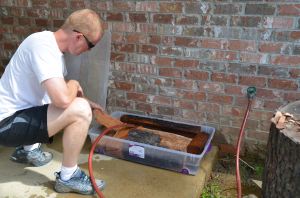
Here’s a good “green woodworking” tip for those of us who don’t have time to use a whole log before it dries. Wet your wood. Get the pieces to rough size and soak them in any type of container that will hold them and water. Here I used a plastic bin that was sold as a wrapping paper storage system. If the wood is pretty dry, leave it here as long as you can (at least 2 weeks). Reconstituted wood is not the same as fresh green, but it’s better than dry.

Once you have re-wet the spoon sized blank of wood, get in front of a crowd of about 30 woodworkers to finish the job. Ok, you can do this alone but it’s way more fun with others. Toward the end of summer I was invited to speak to a woodworking club in Tupelo, Mississippi (just down the road from home in Hernando). The organizer, Marty, asked me to come speak to them. I convinced him that I had nothing interesting to say, but I would be glad to show them how I carved a spatula. This idea caught on and the club members really turned up in force to watch.

Back to the process – Work the blank to something that is rather flat. This flat is where you draw the profile of the spatula. It’s really helpful to draw a centerline and the shape to guide your eyes. Notice that I’ve left waste wood beyond the big end to hold in the clamp. The shaving horse has so much clamping force that this wood will inevitably get deformed. Now, carve away, starting with the areas that require the most removal.

I really like the low profile head of this shaving horse. It lets me work easily on both sides of the head which is very handy for carving! Flip the spatula around a few times and remove wood from anywhere that needs to be lightened. As the spatula gets thinner the work gets more interesting (and risky). Starting with split wood, rather than sawn, makes these thin components stronger than they look.

When the carving is complete, cut the spatula to length and finish up. Give the spatula to one of your new friends, or keep it for your spouse in appreciation for her letting you do a little woodworking on Saturday. With the spatula complete, it’s time for some family adventure.

Yes, it’s a long bike. Yes, we get a lot of funny looks.

If you find yourself in the Tupelo, MS area with some free time, I highly suggest bringing your bicycle. After the spatula carving demo my whole family went on a bike ride on the Tanglefoot Trail. We only did 8 miles, but the trail is over 40 miles, it’s mostly flat, and it’s paved!

Not a bicyclist? No problem. New Albany (trailhead for Tanglefoot) has a great little family friendly restaurant in their picture perfect downtown. Fat Luey’s serves up some great catfish tacos (a new personal Mississippi favorite) and sweet potato fries. Seriously great food.

Curious about my next woodworking event? No need to wait, it will be this weekend. Yep, on Halloween day (2015) I’m giving a free demo at the Woodwork Shop on making three legged stools. The process is super simple and requires few tools. I hope to see some blog readers there, just don’t be late. I’ve got three little girls that need to beg for obscene amounts of candy from neighbors.
Bob Jones